Pollution Prevention
Policy and Basic Approach
As economic development progresses around the globe, pollution issues such as chemical spills, water pollution and soil contamination, air pollution resulting from hazardous waste, and ocean pollution have become serious issues. In response, countries around the world are advancing preventive measures and formulating various standards and laws. Sojitz believes that it is extremely important to reduce its environmental impact and conserve the environment by preventing pollution, curbing waste, recycling, and reusing resources as part of its corporate responsibility in the course of its business activities.
For Sojitz Group, which is engaged in a variety of businesses around the world, including handling various chemicals and materials, preventing pollution is one of the most fundamental and critical aspects of ensuring the sustainability of our businesses. Sojitz Group promotes a wide variety of initiatives related to pollution prevention with the aim of fulfilling its responsibility to society.
One of Sojitz’s Key Sustainability Issues (Materiality) is Environment “contribute to the global environment through our businesses.” As a component of these efforts, Sojitz "strives to preserve the environment and create businesses that are both highly competitive and environmentally friendly by pursuing environmental sustainability in its businesses.” Furthermore, as outlined item 2, “Minimize Environmental Burden” and item 4, “Consider the Environment in New Businesses” of Sojitz’s Environmental Policy, Sojitz will work to "reduce the burden on the environment and prevent pollution.”
Read more
Goals and Targets
Pollution Prevention
In its chemical business, Sojitz Group aims to (1) comply with relevant laws and regulations concerning various chemical substances, (2) prevent accidents by promoting safety management, and (3) conduct corporate activities and actions in consideration of the environment. In order to ensure that there are no omissions in the handling of chemical substances at related business sites, we have created manuals with specific procedures. These manuals stipulate the guidelines for handling chemicals, the relevant laws to be observed, and how to deal with hazardous substances.
In addition, we strive to prevent accidents from occurring and to minimize damage in the event of an accident by establishing systems to manage chemical substances and for responding to emergencies.
Compliance with Environmental Laws and Regulations
We remain apprised of the applicable laws and regulations to regularly confirm compliance conditions not only at Sojitz Corporation, but also at our Group companies. Internal audits of our Group companies also include checks on these compliance conditions.
Promoting Employee Awareness
We will make this policy known to all executives and employees, and continue to carry out educational and awareness-raising activities.
Systems
The Sustainability Committee discusses the formulation of company-wide policies and targets related to sustainability, including pollution prevention, the establishment and maintenance of systems to implement these policies, and monitoring various measures that utilize the ISO 14001 environmental management system standard. The Sustainability Committee reports to the Management Committee and Board of Directors, and receives supervision and direction from the Board of Directors.
In addition, the Finance & Investment Deliberation Council, which deliberates investments and loans, checks individual proposals for their relevance in terms of sustainability and environmental and social (human rights) risks. Furthermore, the Investor Relations & Corporate Sustainability Department, a dedicated body, is in charge of monitoring the policies and targets formulated by the Sustainability Committee, as well as environmental and social (human rights) risks.
Sustainability Committee Members (Current as of April 1, 2025)
Committee Chair |
|
---|---|
Members |
|
Observers |
|
Secretariat |
|
Systems to Promote and Implement Sustainability
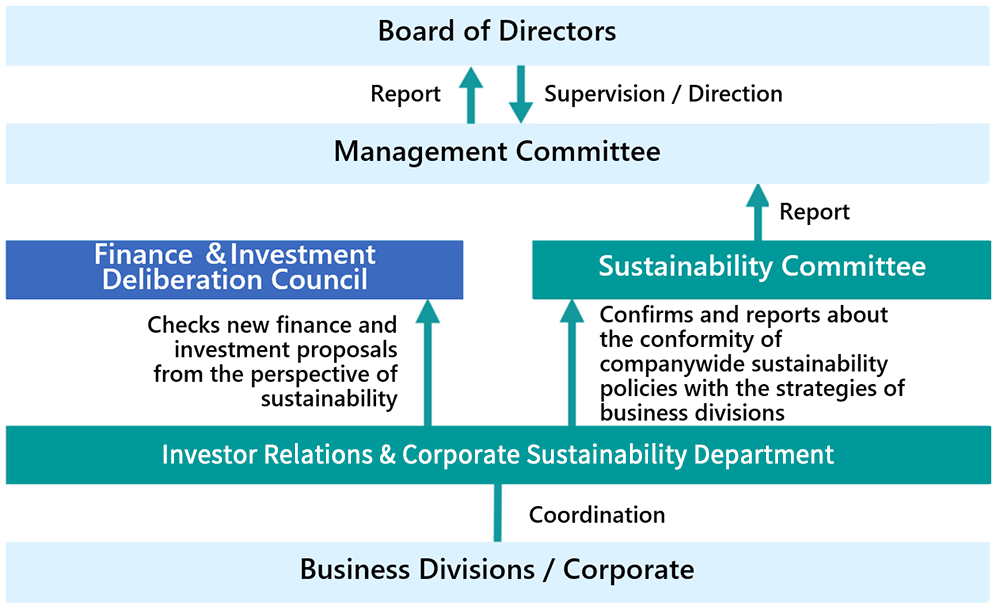
Risk Management Systems
Quality Management Policy
Sojitz develops operations in a wide range of fields to fulfill its mission as a general trading company: delivering goods and services where there is a need. Our value chain spans from resource development through to production, processing, wholesale, distribution, and finally retail sales and service provision.
We have established the Sojitz Group Quality Management Policy to define basic principles for quality management that we expect to be observed on a company-wide basis. Guided by this policy, Sojitz practices quality management at the frontline organizations that interact directly with customers. We thereby seek to provide our customers and society with safe and reliable goods and services.
Read more
Environmental and Social Risk Management in New Business
-
Prior to deliberating on new investment and loan projects, we require the department applying for investment and loan approval to complete an “Environmental and Social Risk Checklist.” The department works to prevent environmental pollution by using the checklist to ensure that they conduct the necessary due diligence regarding all potential risks, such as soil, groundwater, or water contamination.
-
Monitoring Existing Businesses
Through external and internal analysis, we identify business areas that pose a high risk of environmental and wastewater pollution from among Sojitz Group businesses, including Group companies (consolidated subsidiaries and holding companies) and business partners, and analyze where environmental and social issues are generally prone to occur throughout entire supply chains from upstream to downstream. Moving forward, we will continue to implement the PDCA (Plan-Do-Check-Action) cycle for risk response based on third-party opinions from external experts, maintain a high level of awareness of environmental issues throughout the Group, and strengthen our initiatives for identifying new risks.
In addition, Sojitz Corporation has acquired ISO 14001 certification, the international standard for environmental management. We will also conduct monitoring from the perspective of our pollution prevention efforts.
ISO14001 Monitoring
Confirming Compliance with Laws and Regulations
We confirm that all Sojitz departments and target Group companies comply with the laws and regulations related to chemical substances and anti-pollution measures, such as RoHS regulations, REACH regulations, and industrial waste laws. Sojitz’s president serves as the chair of the Sustainability Committee, which confirms issues such as whether Sojitz is in compliance with these anti-pollution laws and regulations, and carries out management reviews to provide corrective instruction.
Establishing Action Plans for Departments and Offices
The policies and items resolved by the Sustainability Committee and reported to the Management Committee and Board of Directors are made known to employees not only through the company intranet, but also through regularly held briefing sessions with each department, organized by the Sustainability Committee secretariat.
Items resolved by the Sustainability Committee are established by each department and office at the beginning of the period. These consist of 1) environmental impact of business activities around the world, and an analysis of related laws and regulations; and 2) goal setting and action plans to mitigate these environmental impacts, including those related to pollution prevention. These items are reviewed by each department and office every six months, and the results of these reviews are evaluated by the Sustainability Committee and reported to the Management Committee at the beginning of the following year.
Safety Management in the Chemicals Business
The Chemicals Division implements the following safety management system in line with the aforementioned policies and targets set out by Sojitz Group.
Compliance with Chemicals Management Regulations and Sojitz Safety Initiatives
The Chemicals Division has established a set of policies regarding the handling of chemicals that includes the Chemicals Management Guidelines and the Chemicals Management Regulations—a document created in accordance with current chemicals-related laws and regulations. The Chemicals Division keeps division members informed regarding their content through ongoing training initiatives and maintains the following records: an organizational chart for the Sojitz chemicals management system, a record of all approved chemicals, a registry of employees bearing legal liability in chemicals-related matters, and an emergency contact chart.
The Chemicals Division ensures strict compliance with a wide range of laws and regulations relating to environmental management systems, including Japan’s Chemical Substances Control Law, Industrial Safety and Health Act, PRTR Act, Poisonous and Deleterious Substances Control Act, Fire Service Act, and High-Pressure Gas Safety Act.
Sojitz provides a Safety Data Sheet (SDS) for each chemical product it handles in order to appropriately notify all business partners throughout the company’s supply chains regarding the hazard and toxicity information for each product. For imported products, Sojitz also includes the appropriate labeling in accordance with Japanese laws and requirements to ensure that end users can use the products safely. SDSs include information on relevant environment protection-related laws and regulations including the PCB Special Measures Law, Fluorocarbon Emissions Control Act, Water Pollution Prevention Act, Soil Contamination Countermeasures Act, Air Pollution Control Act, and Offensive Odor Control Law.
No violations of environment-related laws and regulations were reported at Sojitz Group in FY2024.
Centralized Management of Chemical Products
The Chemicals Division centrally manages all chemical products handled by Sojitz Group. The CAS registry number and content percentage for each chemical compound contained in a chemical product are listed on each product’s SDS, and this information is compiled in a central list maintained by the Chemicals Division. This system allows employees to quickly identify which products are subject to specific regulations, such as the Industrial Safety and Health Act, PRTR Act, or Poisonous and Deleterious Substances Control Act. Employees can also easily identify and implement the necessary response in the event of a revision to a law or regulation.
Chemicals Management Training
The Chemicals Division conducts ongoing trainings and seminars for all employees on chemicals management and environment-related laws and regulations. In FY2024, a total of roughly 211 employees participated in chemicals management trainings both in person and online.
As part of initiatives to improve employees’ chemicals expertise, we hold small, in-person training for key topics. These trainings are held over multiple sessions and are adapted to match the skill levels and requirements of the participants.
(Current as of March 2025)
Training | Participants |
---|---|
New employee training: Basics of chemicals management | 25 |
Introductory training: Import/export trade and registration of chemical substances | 34 |
E-learning: Company policies on chemicals management | 208 |
Basic and practical training: Management of poisonous and deleterious substances | 88 |
On-site training at chemical tank operating company | 15 |
Chemicals Requiring Gradual Phase-Out
The Chemicals Division does not handle any chemicals that require a gradual phase-out.
Use and Management of Substitutes for Substances of Concern
The Chemicals Division has no history of utilizing substitutes for substances of concern.
Environmental Incidents and Risk Management System: Initial Reporting Process (IPPOU)
The Chemicals Division has established a system for ensuring prompt reporting to relevant departments and regulatory authorities in the event of an unexpected chemicals-related incident. Sojitz’s chemicals management organizational chart and emergency contact chart enable those on site to quickly report any incident to management and other relevant departments, identify the cause, take appropriate corrective measures, and consider future preventative measures. Through this system, the Chemicals Division aims to minimize the spread of damages and to be thorough in imple menting prevention strategies.
There were no environment-related incidents at Sojitz Corporation and Group consolidated subsidiaries in FY2024.
Initiatives
Based on the aforementioned policies, Sojitz Group implements various initiatives to prevent pollution as describe below.
Initiatives at NI Chemical Corporation
-
NI Chemical Corporation is a Sojitz Group subsidiary involved in the chemical and oil tank leasing business. The company also stores toxic and hazardous materials, primarily including flammable liquids. These are some of NI Chemical’s anti-pollution measures and environmental initiatives.
-
1) VOC Measures
-
Volatile organic compounds (VOC) impact the level of photochemical oxidants (*1), and NI Chemical uses a device to collect VOC to reduce emissions into the atmosphere.
VOC collected: FY2021 (83 ton) , FY2022 (76 ton) , FY2023 (93 ton)(*1) Photochemical oxidant is the general term given to substances created by a photochemical reaction that occurs when VOC or other compounds are hit by ultraviolet rays from the sun. If the concentration of photochemical oxidants rises, it can result in photochemical smog, or white, mist-like air that can cause irritation to the eyes or throat and other health hazards.
-
2) Management of Hazardous Waste
-
When cleaning tanks, hazardous waste is at times present, including certain chemicals that are highly flammable. Hazardous waste is stored in a specific storage area that follows all waste regulations pertaining to storage, management, and disposal.
In terms of the Waste Management and Public Cleaning Law, NI Chemical is required to submit an industrial waste disposal plan that includes the disposal of hazardous waste as well as submit its disposal records. The company monitors waste management according to this plan and reports to the government. Additionally, NI Chemical implements innovative measures for tank cleaning as well as ways to reduce residue buildup that would require cleaning in order to minimize the production of industrial waste. -
3) Installation of Oil Fences
-
NI Chemical transfers chemical raw materials owned by its customers from tanker ships to tanks on open water. In the unlikely event of a chemical spill, NI Chemical has an oil fence installed on-site to prevent sea pollution.
NI Chemical has also established a joint organization to prevent maritime disasters, and in the unlikely event of an accident will make use of the organization’s oil boom extender.
NI Chemical has no record of ocean pollution or pollution incidents to date. -
4) Establishment of a joint maritime disaster prevention organization with neighboring companies
-
Disaster drills are held regularly.
Partnering with neighboring companies, NI Chemical has established a joint maritime disaster prevention organization, which regularly holds joint drills that include flood control and other practices to strengthen its disaster prevention capabilities.This joint organization owns two fire engines and has three people stationed on duty at all times throughout the year.
-
5) ISO9001
In order to maintain quality control, safety standards, and efficient handling of chemical products, NI Chemical obtained ISO9001: 2015 certification and strives to maintain certification for 20 years.
Performance
■ Waste Discharge
Sojitz Corporation’s Waste Discharge and Recycling Rates
1. Data and Results
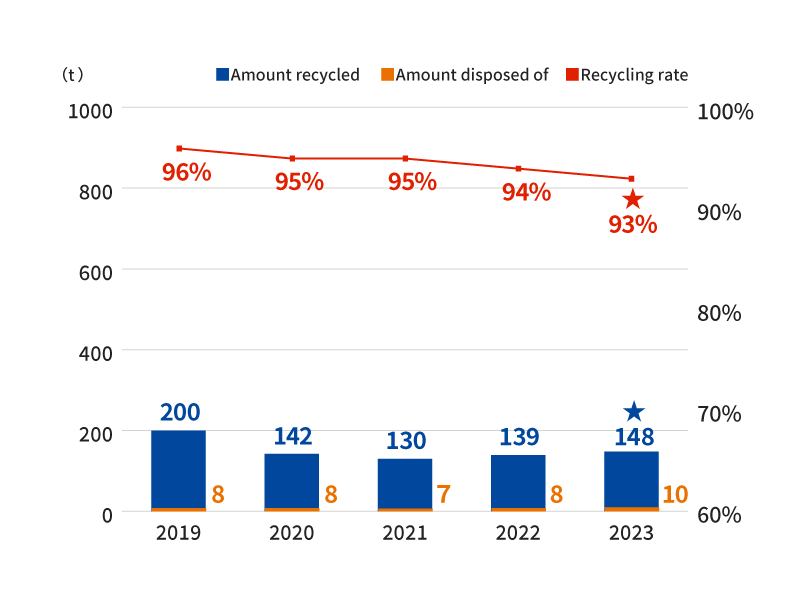
2. Boundary of Data
Sojitz Corporation: Head office, Kansai Office, excluding branches (Hokkaido, Tohoku and Nagoya)
3. Target Recycling Rate
Office recycling target: Maintain a recycling rate of 90% for office waste.
4. Hazardous waste
(unit:t)
FY2019 | FY2020 | FY2021 | FY2022 | FY2023 | FY2024 | |
---|---|---|---|---|---|---|
Hazardous waste* | 0.02 | 0.02 | 0.13 | 0.03 | 0.02 | 0.03 |
- The total amount of specially controlled industrial waste generated by Sojitz Corporation.
Sojitz Group’s Waste Discharge
1. Data and Results
(unit:t)
FY2019 | FY2020 | FY2021 | FY2022 | FY2023 | FY2024 | |
---|---|---|---|---|---|---|
Waste Discharge | 60,485 | 67,711 | 62,769 | 67,103 | 76,829 | 76,785 ★ |
-Amount recycled | 8,281 | 7,100 | 18,000 | 32,939 | 15,736 | 10,851 |
-Amount disposed of | 52,203 | 60,611 | 44,768 | 34,163 | 61,093 | 67,935 |
2. Boundary of Data
Sojitz Corporation, all domestic and overseas consolidated subsidiaries, and unincorporated joint ventures subject to reporting under the operational control approach
■ Other Environmental Data
Sojitz Group's NOx, SOx and VOC Emissions
(unit:t)
FY2019 | FY2020 | FY2021 | FY2022 | FY2023 | FY2024 | |
---|---|---|---|---|---|---|
NOX (Nitrogen Oxides) | 2,632 | 1,704 | 2,255 | 2,516 | 1,656 | 1,348 |
SOX (Sulfur Oxides) | 408 | 593 | 358 | 717 | 518 | 152 |
VOC (Volatile Organic Compounds) | 127 | 138 | 210 | 195 | 195 | 180 |
Number of incidents or violations by Sojitz Group concerning water intake and discharge
FY2024: 0 cases
Environmental Education
In order to implement our EMS, we hold a company-wide briefing session on the ISO14001 standard at the beginning of each fiscal year. In addition, we conduct trainings for internal environmental audit personnel, e-learnings for select employees on environmental laws and regulations concerning topics such as industrial waste disposal, and departmental education activities twice a year for all employees in all our organizations in order to raise awareness and impart specialized knowledge. Sojitz continues to encourage employees to take the Certification Test for Environmental Specialists (Eco Test), a certification test administered by the Tokyo Chamber of Commerce and Industry. In total, 164 Sojitz employees have received the certification.
Environmental Education Trainings in FY2024 (for employees at Tokyo HQ and select Group companies)
Training | Target employees | Number of participants |
---|---|---|
Environmental education (held departmentally twice a year) | All employees | Approx. 3,100 |
E-learning course on waste management laws | Employees involved in waste management and regulatory reporting | 1,120 |
Trainings for internal environmental audit personnel | Candidates for internal environmental audit roles | 41 |